Floating seals and skeleton oil seals are both rapidly developed upgrade products of later seals. Compared with traditional seals, they are specially designed and applied under specific conditions. The following article will help you fully understand the differences between them and help You more professionally select seal options that suit your or your customer’s application.
Table of Contents
Toggle1. The difference between structure and working principle:
Floating seal: Mainly composed of two identical metal rings and two rubber rings. During operation, the relative sliding between the metal ring and the rubber ring forms a sealing space. At the same time, the rubber ring deforms under the action of external media, generating a pressing force on the metal ring, thereby ensuring the sealing effect. The floating oil seal can automatically adjust during rotation to accommodate shaft eccentricity and vibration. A floating oil seal is a combined floating seal created around the shaft that generally surrounds the lubricant, allowing wear and leakage at the same time as the lubricant returns to the tank. Its structure is straightforward, consisting of two primary materials: a plastic or rubber shell and a metal casing. Rubber or plastic parts are used to create the seal, while metal parts are used to maintain its integrity.
Oil seal: usually composed of a metal skeleton and a rubber sealing lip. The skeleton serves as a supporting structure to help fix the rubber sealing lip so that it can maintain its shape on the shaft and generate pressure in contact with the sealing lip to achieve a sealing effect. It creates a static seal around the shaft or lug. Its internal structure is a combination of skeleton + elastic material. The flexible material needs to be forced into the belt groove through the skeleton to prevent it from “loosening”, thereby achieving the purpose of sealing. Skeleton oil seals are suitable for high-speed rotating equipment, such as generators, gearboxes, etc.
2. The difference between design and use:
Floating seal: The design is relatively simple and easy to manufacture and repair in the factory. Although its structure is simple, its sealing performance and wear resistance may be slightly inferior to the skeleton oil seal. Floating oil seals are mainly used in low-speed and heavy-load applications, such as the left and suitable drums of continuous coal mining machines.
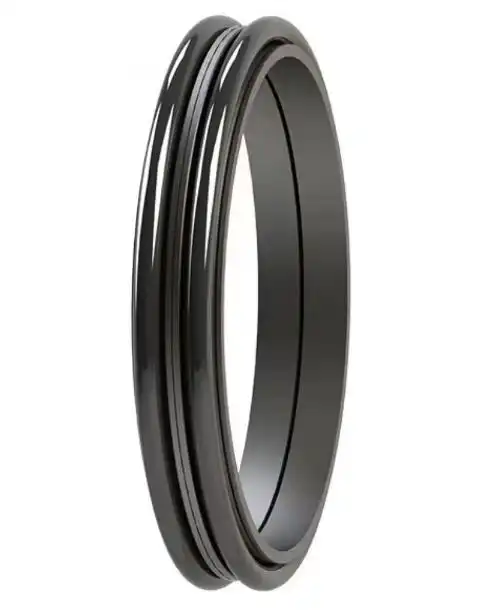
Oil seal: There are various designs, including single-lip and double-lip skeleton oil seals, and classification according to the skeleton type and different working conditions (such as rotating or reciprocating type). Skeleton oil seals are widely used in automobile engines, diesel engines, gearboxes, differentials and other equipment.

3. Differences in production materials:
Floating seal: mainly composed of plastic or rubber shell, metal shell, lubricating oil or other lubricating substances and other materials. The combination of these materials can be selected depending on the application to suit the working conditions better.
Oil seal: The primary material is elastic material, such as NBR, HNBR, PU, etc. The primary material of the skeleton is steel wire. These materials can withstand long-term work under high load conditions such as high temperature, high pressure and low temperature.
4. Differences in applicable working conditions:
Floating seal: It is suitable for low-speed and high-pressure environments and is suitable for environmental wear situations. Because its design allows a certain degree of wear, it can automatically compensate for the wear of the sealing end through the flow of oil, so it can effectively reduce the wear and tear of machinery and equipment. Damage.
Oil seal: suitable for high-speed rotating environments because it is designed to resist centrifugal force during high-speed rotation and maintain the sealing effect. Skeleton oil seals are mainly used to prevent lubricant leakage in machinery and equipment, such as automobile axles, engines and gearboxes. Skeleton sealing rings are the most mainstream sealing technology in the automotive and heavy machinery industries.
To sum up, both oil seals and floating seals are mechanical seals, but there are some differences in their structures, materials, applications, etc., and they are suitable for different working conditions and equipment. In actual applications, appropriate mechanical seals should be selected based on specific application requirements.