Matching operating parameters
It is necessary to fully understand the specific parameters of the hydraulic system where the seal will be applied,including the hydraulic cylinder’s motion state, velocity, pressure range, temperature fluctuation range, hydraulic medium, etc. These characteristics have a direct bearing on the structural design and choice of seal material.
Assessment of application’s environmental adaptability
It is also important to clarify the system’s operating environment – whether it is a static seal or dynamic reciprocating motion, whether there are impact pressures, whether the usage location is indoors clean or polluted with dust and contaminants etc. This concerns the seal mechanism design.
Testing for material compatibility
Seal service life is directly impacted by the compatibility of the seal material. To verify that elastomeric seals are compatible with the particular hydraulic medium, material compatibility tests using established techniques, such ASTM, must be carried out.
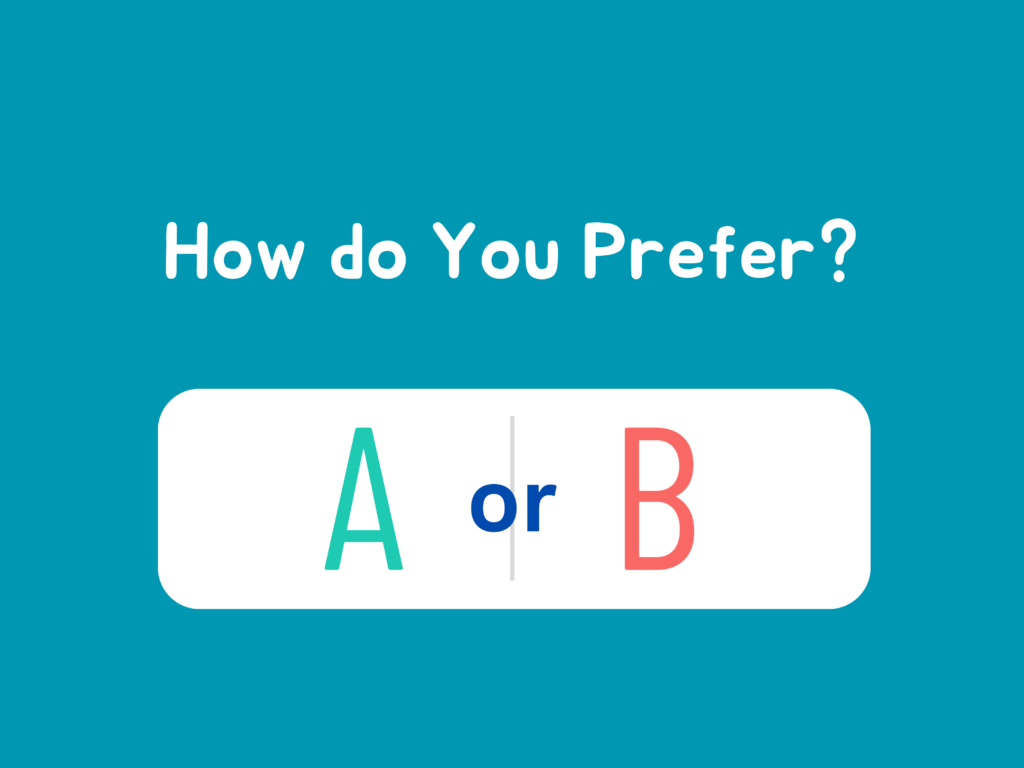
Validation and testing
When testing samples in rotating and reciprocating motion,Dependable test rigs must methodically record hydraulic cylinder seals wear levels, friction heating effects,temperature spikes, and dependability tests under all working situations. recovery rates, and hydraulic oil seal pressure retention capacity across complete machine operating cycles exposing hydraulic cylinder seals to worst use conditions. Extensive hydraulic cylinder seals testing verifies hydraulic cylinder seals materials compatibility using established hydraulic oil seal evaluation techniques to identify suitable elastomers.
Strict statistically significant test results from carefully planned experiments offer a reliable foundation for choosing hydraulic cylinder seals.
Certification of quality systems
Choose reputable brands that have been approved by quality assurance programs like ISO 9001. Consistent product performance is ensured by strict quality process control.
It is crucial to match the operating characteristics of the seals, evaluate environmental compatibility, verify material performance, carry out rigorous testing, and find reliable, certified providers of hydraulic cylinder seals when choosing hydraulic cylinder seals for hydraulic systems.
As a reputable seals manufacturer with stringent quality assurance practices producing reliable hydraulic seals, TYS Sealing Solutions offers discerning buyers with high-quality products at competitive prices.
Having obtained ISO 9001 certification,TYS applies uniform process control throughout the whole manufacturing cycle, from the first meterials (TYS good at PTFE,PU,NBR,FKM ,COMPOSITE meterials and other compounds of the seals,eg ptfe seals) to the last inspection and testing of hydraulic cylinder seals. This globably recognized quality system also extends to the critical supplier management functions for sourcing of raw materials incorporated into their finished hyd cylinder seals.
In conclusion, the selection of high-performance hydraulic seals is based on their track record of dependable performance throughout their entire lifespan, particularly in given operating conditions. Designs like molded rubber materials and oil seal profiles are tested to meet specified applications without premature failure. Confidence in continuous sealing capability is increased by meticulously verifying material data and the oil seal’s ongoing resistance to real-world elements like abrasion, temperature extremes, and fluid chemical compatibility.