In the after-sales maintenance market of mechanical equipment, when maintenance engineers determine that the seal is damaged, for the sake of overall system efficiency, they often directly replace the entire set of seals in the hydraulic cylinder instead of just replacing a certain seal.
Because the price of the seal is relatively cheap and the labor cost and downtime cost of replacement are higher, so it is more cost-effective to choose a one-time direct replacement of a new hydraulic seal kit.
This article will help you fully analyze the hydraulic seal kit, from the basic types of hydraulic seal kits to customized hydraulic seal kits.
Table of Contents
ToggleWhat types of hydraulic seals are in a seal kit?
A hydraulic seal kit typically contains various types of seals designed to prevent fluid leakage, maintain pressure, and ensure safety operation of hydraulic systems. The main types of hydraulic seals found in a seal kit include:
Rod Seals – Prevent hydraulic fluid leakage from the cylinder along the rod.
Piston Seals – Create a seal between the piston and cylinder bore to prevent fluid bypass.
Wiper Seals (Scraper Seals) – Remove dirt, dust, and debris from the rod to prevent contamination.
O-Rings – Provide static sealing in various areas of the hydraulic system.
Backup Rings – Support O-rings to prevent extrusion under high pressure.
Wear Rings (Guide Rings) – Prevent metal-to-metal contact between moving parts, reducing wear and friction.
Static Seals – Used in non-moving parts to prevent leakage at joints and fittings.
Buffer Seals – Absorb pressure spikes and help extend the life of rod seals.
The above are the types of hydraulic seal kits required for hydraulic cylinders. You would like to choose the specific combination based on the actual application.
How do you know if a hydraulic seal kit will fit your system?
To determine if a hydraulic seal kit will fit your system, follow the step-by-step for your reference:
1. Identify the Hydraulic Component
Determine the type of hydraulic component (e.g., cylinder, pump, valve, or motor) that requires the seal kit.
Check the equipment’s manufacturer and model number. This information is often found on a nameplate or stamped on the component.
2. Check the Seal Kit Part Number
Look for the part number of the existing seal kit or the component itself. This can often be found on the manufacturer’s website, or you can contact the hydraulic component manufacturer or a trusted seal kit supplier with the component details and measurements. They can confirm compatibility and recommend the correct seal kit.
Cross-reference the part number with the seal kit part number to ensure compatibility.
3. Measure the Seal Dimensions
If the part number is unavailable, measure the dimensions of the existing seals, including:
Shaft diameter (for rod seals)
Bore diameter (for piston seals)
Seal width (cross-sectional thickness)
Groove dimensions (if applicable)
Compare these measurements with the specifications of the seal kit to ensure the new seals match exactly.
4. Verify Seal Type and Material
Ensure the seal kit includes the correct type of seals (e.g., rod seals, piston seals, wipers, O-rings) for your component that matches your hydraulic system’s design.
Check that the seal material (e.g., nitrile,ptfe, polyurethane, Viton) is compatible with the hydraulic fluid and operating conditions (temperature, pressure, and environment).
5. Check for OEM or Aftermarket Compatibility
Determine if the seal kit is an OEM (Original Equipment Manufacturer) part or an aftermarket equivalent. OEM kits are guaranteed to fit, while aftermarket kits must match your specifications precisely.
6. Inspect the Old Seals
If possible, compare the old seals with the new ones in the kit to ensure they match in size, shape, and design.
7 . Review System Pressure Ratings
Ensure the seals can withstand the working pressure or temperature of your hydraulic system to prevent failure or leaks.
8. Test Fit Before Assembly
Before final installation, conduct a dry fit to check alignment and dimensions.
If you are unsure, please contact a reliable hydraulic seal kit supplier or us to help you get the right product. Once you understand the types of hydraulic seal kits and whether the seal kit you choose is suitable for your system, you can use it with confidence to ensure the normal operation of your equipment.
If you want to learn about common hydraulic seal kit issues and leakage troubleshooting methods, click here to access the article.
What are the benefits of high-quality hydraulic seal kits?
High-quality hydraulic seal kits play a decisive role in the reliability, service life, and performance improvement of hydraulic systems. Here are the main benefits of using high-quality hydraulic seal kits:
1. Improved sealing performance, reduced risk of leakage
High-quality seals are made from premium materials such as PTFE, fluororubber (FKM), and polyurethane (PU), combined with precise machining processes. They effectively reduce hydraulic oil leakage, ensure excellent sealing performance, improve system efficiency, and minimize environmental pollution.
2. Reduced maintenance costs, improved economic benefits
Less downtime: The reliability of high-quality seals reduces failures and equipment downtime caused by leakage or seal damage, improving production efficiency.
Lower replacement frequency: Compared to ordinary hydraulic seals, high-quality seals have a longer lifespan, reducing replacement frequency and maintenance costs.
Reduced hydraulic oil loss: Less leakage means less hydraulic oil waste, lowering overall operating costs.
3. Extended equipment service life
High-quality seal materials can withstand harsh environments such as high frequency, high speed, high pressure, and high temperature. They are more wear-resistant and less prone to aging.
Premium materials can resist corrosion from hydraulic oil, strong acids, alkalis, and other chemicals, reducing premature failure due to material degradation, thereby extending the service life of seals and equipment.
4. Adaptability to more demanding working conditions
High-quality hydraulic seal kits can adapt to various extreme conditions, such as high temperatures above 200°C and high-pressure hydraulic systems (e.g., over 50 MPa). Some high-end materials (e.g., PTFE composites) maintain good flexibility and sealing performance even in low-temperature environments. Specially designed seals can withstand high-frequency vibrations and impact loads, avoiding seal failure caused by vibrations and ensuring excellent sealing performance under high pressure, high temperature, and complex conditions.
5. Wide range of industry applications
High-quality hydraulic seal kits are widely used in the following industries:
Construction machinery (excavators, loaders, bulldozers)
Metallurgy and heavy industry (hydraulic presses, steel manufacturing equipment)
Oil and gas (high-pressure valves, drilling equipment)
Aerospace (aircraft landing gear, hydraulic control systems)
Food and medical industries (FDA-compliant hydraulic seals for contamination-free environments)
In practice use, although high-quality hydraulic seal kits are more expensive, their advantages are more. In the long time to evaluate, they can reduce overall costs. TYS SEALS continues to produce high-quality hydraulic seal kits, offering competitive prices to meet the needs of high-end industries and gaining recognition from global customers.
Are hydraulic seal kits available for custom designs? Can I buy custom hydraulic seal kits?
The answer is yes, hydraulic seal kits can be custom-designed, and you can purchase custom hydraulic seals to meet specific application requirements. Custom seals are typically used for special working conditions, such as high temperature, high pressure, special media, or specific equipment and unusually large size requirements.
1. Feasibility of custom hydraulic seal kits
Many professional hydraulic seal manufacturers (including industrial seal producers like TYS) can provide custom hydraulic seal kits. Common customization needs include:
Special size customization: If standard sizes do not meet equipment requirements, seals of specific sizes can be customized. TYS can produce large-size hydraulic seals ranging from 30-1400 mm to meet your needs. For example, TYS has customized oversized PTFE seals for valves in the oil and gas industry.
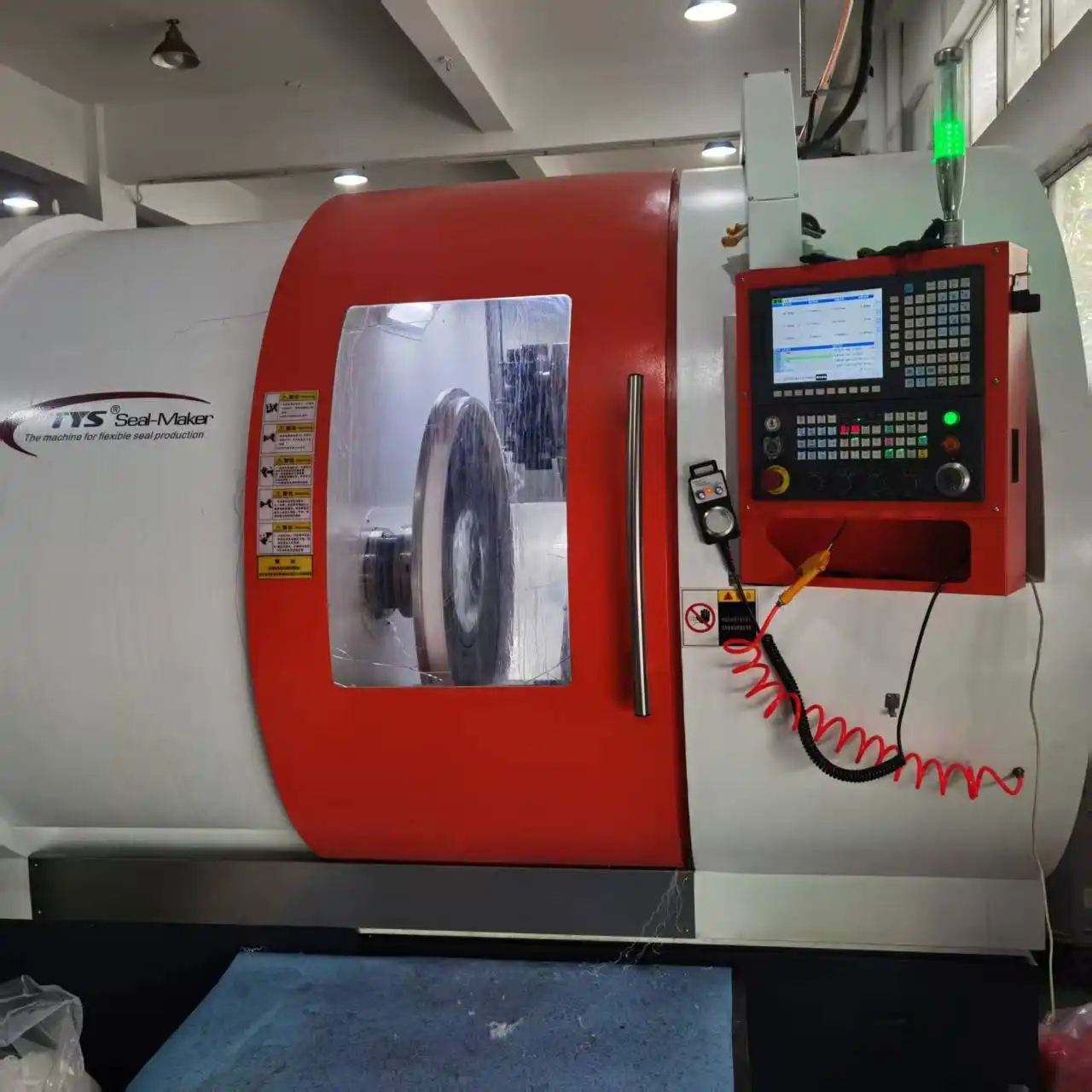
Special material customization: Specific materials can be selected for high temperature, high pressure, strong corrosion resistance, or low friction requirements.
Special seal structure customization: Special-shaped seals, such as composite seals or double-lip seals, can be designed according to equipment needs.
Specific industry applications: Seals compliant with FDA, ISO, and other standards can be provided for industries such as food, medical, petrochemical, and aerospace.
If you have other special customization needs, consult a seal manufacturer for solutions.
2. How to purchase custom hydraulic seals
If you need custom hydraulic seal kits, you can purchase them through the following methods:
1)Contact a seal manufacturer or supplier
You can contact seal manufacturers directly, such as TYS SEALS or Voneseals, etc, China hydraulic seals manufacturer or international manufacturers like Parker, Trelleborg, or Freudenberg, and provide your specific requirements.
Alternatively, you can work with agents or distributors who offer custom seal services.
2)Provide customization parameters
When customizing seals, you need to provide the following information:
Size parameters: Provide technical drawings with seal inner diameter (ID), outer diameter (OD), height (H), and groove dimensions.
Working environment: Specify the operating conditions, such as temperature range, pressure range, and presence of special media (e.g., strong acids, alkalis, or fuels).
Motion type: Confirm whether the seal is used for reciprocating motion, rotary motion, or static sealing.
Material requirements: Specify if wear-resistant, high-temperature-resistant, chemical-resistant, or low-friction materials are needed.
Quantity requirements: Provide the quantity of custom seals required for a price estimate.
3)Confirm samples and production lead time
Suppliers usually provide samples for testing to confirm the suitability and quality of the seals.
Before mass production, you can conduct a small trial batch to ensure the seals meet your requirements.
The production lead time varies depending on complexity, typically ranging from 3-10 days (CNC machining) to 2-4 weeks (mold production).
Hydraulic seal kits play an important role in the after-sales maintenance market for mechanical equipment, providing convenient replacements and reducing downtime. Get the correct seal kit for specific hydraulic applications and finding a reliable hydraulic seal kit supplier are important too. I wishing you have reliable hydraulic seal kits!