A lip seal is a product used to seal low-pressure media. The typical lip seal structure is shown in Figure 1. Leakage is the primary manifestation of seal failure, but the cause of leakage is not a single one; it is more due to the combined effect of multiple factors. If you want to understand the cause of seal failure, you must get at least the shaft or the seal. The best case is to observe the seal failure phenomenon and characteristics on-site and witness the process of removing the seal from the shaft on-site.
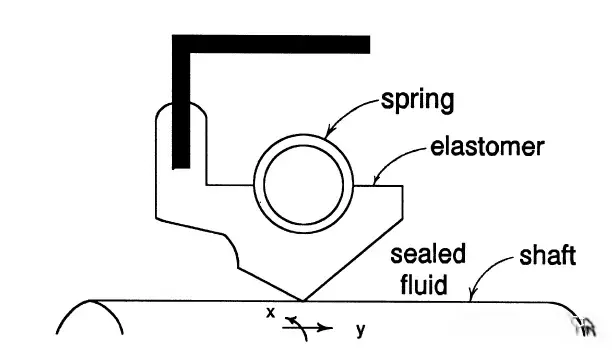
Based on experimental data, through the failure analysis of seals with working time less than 100 hours or service performance less than 10,000 km, it is believed that typical failures include:
30%: Problems in shaft design and manufacturing process;
30%: Incorrect assembly of the shaft and seal ring;
10%: Wrong seal ring selection;
15%: Other reasons, such as incompatible lubricant, excessive temperature rise, vibration, excessive dirt, and dust.
15%: Early apparent leakage.
The following are the main failure manifestations and leading causes:
(1) The sealing ring has no significant damage and no debris
The interference is insufficient, or a spring needs to be used;
High-viscosity lubricants cause excessive oil film;
Mechanical wires on the shaft causing oil leakage;
Excessive use of grease can lead to leakage.
(2) Mechanical damage to the sealing lip
The shaft or mounting groove scratches the sealing lip;
Scratches caused by grooves and gears during installation;
Insufficient assembly tools;
Insufficient protective measures lead to shaft damage;
Plastic seals, such as PTFE, are more susceptible to scratching. Insufficient protective measures can easily lead to a significant increase in the probability of injury.
(3) Carbon deposits on and around the sealing lip
Carbon deposition is mainly caused by the high-temperature rise of the oil film in the contact area. Relatively light carbon deposits tend to be found in the lip area near the air side. When the temperature rises too high, and carbon deposition is severe, it will often interfere with the sealing lip, causing leakage. Improvement measures: Improve the system’s heat transfer performance, reduce friction, and replace high-temperature-resistant lubricating oil.
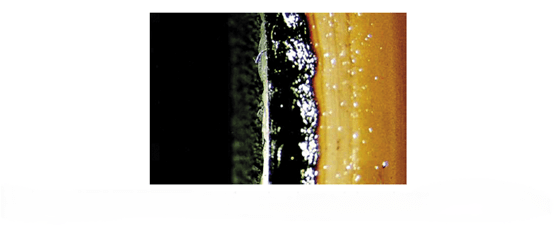
(4) Axial cracks on the sealing lip
Axial cracks can be acceptable or considerable. Small cracks usually require careful inspection to be discovered. Cracks on the sealing lip are generally believed to be caused by the long-term operation of the sealing lip in a high-temperature environment. High temperature refers to the temperature of the contact area of the sealing lip during operation. High temperature accelerates the aging of the sealing lip. In addition, aging will be more severe under the combined effect of oil and high temperature.
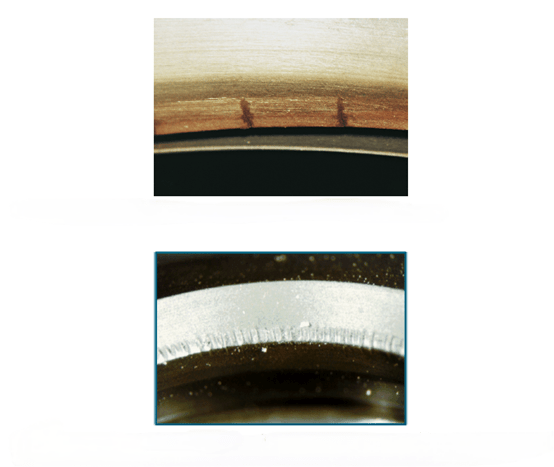
(5) Seal and fluid compatibility
The sealing lip may expand due to the action of sealing fluid or lubricating oil, causing significant deformation. When the sealing medium reacts chemically with the rubber material, bubbling occurs.
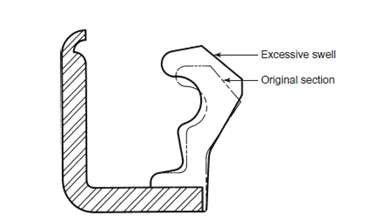
(6) When there is no significant temperature rise, the sealing lip is worn, and debris is in the sealing area.
The fragments in the sealing area indicate that the function of the lip during product design does not meet the requirements;
Metal fragments: It may be due to problems with the cleaning and assembly processes or due to assembly eccentricity;
Dust and impurities: Possibly due to poor storage.
(7) Excessive wear and groove formation
Vast wear tracks and medium-level grooves may be caused by local dry friction operation or operation under high-pressure conditions;
Severe wear of the sealing lip and wear on the shaft surface may be caused by fine abrasive particles on the rotating track;
Severe wear and severe deformation of the sealing lip: often caused by excessive fluid pressure, resulting in severe wear.
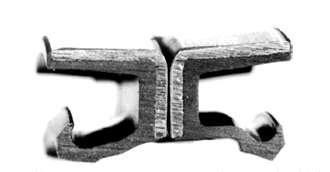
(8) Circumferential damage to the sealing ring
The circumferential fracture of the rubber of the sealing lip is mainly due to the action of alternating stress during the working process.
Conclusion:
The above analysis shows that the sealing ring’s main failure form is leakage, which is usually manifested as wear. The main reason for failure is the temperature rise caused by increased rotational torque. On the one hand, the rise in temperature will cause the rubber material to age rapidly; on the other hand, it will also cause the lubricating oil to carbonize.
TYS has decades of experience in lip seal design and has accumulated a wealth of lip seal technology. To learn more, click on the TYS lip seal product page or contact the TYS team for help.